一、研究背景
锂金属电池有望实现600 Wh kg-1的能量密度目标,以满足电动汽车、电网储能乃至电动航空日益增长的能源需求。尽管厚锂金属负极可实现良好的循环稳定性,但过量的锂会削弱锂金属负极的可行性,并妨碍其在高能电池体系中的实际应用。无负极锂金属电池通过结合含锂正极和无锂负极集流体,避免了锂金属负极的直接使用,具有减少资源消耗、提高安全性及简化制造工艺的优势。然而,这种能量最大化架构会加剧锂损失并缩短电池寿命。锂损失主要源于两方面:(1) 由于(电)化学反应形成固体电解质界面相(SEI);(2) 由于电化学通路切断形成孤立的“死锂”,通常被称为电子绝缘。尽管在抑制锂损失方面已有显著进展,大多数研究仍限于实验室规模的纽扣电池或单层软包电池,且电解质供应充足,这破坏了无负极架构的能量密集特性,并偏离了现实电池条件。在实际应用中,电解液供应有限且持续消耗,导致电解液脱湿,进而加剧锂损失问题,这超出了传统电子绝缘的范畴。因此,重新审视贫电解液下“死锂”的形成机制及存在形式,能够深化我们对电池退化机制的理解,进而推动开发有效的策略来提升锂金属电池的性能。
二、主要内容
近日,华中科技大学孙永明教授等人首次揭示了锂金属电池负极中一种与传统的电子孤立锂(E-iLi)不同的新形式“死锂”——离子孤立锂(I-iLi)。通过对特定健康状态下高比能锂金属软包电池电解液依赖的容量恢复特性进行定量分析,作者阐明了I-iLi源于电解液退浸润引起的离子通路切断。基于此,作者首次提出了电极润湿性的评估标准——电解液浸润率(EFR),其值取决于负极锂沉积物的孔隙率和电解液保留量。为维持高EFR环境并抑制I-iLi的形成,作者进一步引入应力调节来致密化负极锂沉积结构、减缓电解液消耗。例如,将外压从0.1 MPa提升到1 MPa后,高比能软包电池50%健康状态下I-iLi占总锂损失的比例从21%降至1%。根据以上研究结果,进一步制备了安时级无负极LiNi0.95Mn0.03Co0.02O2||Cu软包电池,实现了551 Wh kg-1的高能量密度,并在0.2 C下充放电循环100圈后保持70%的容量。这一成果标志着可充电无负极/锂金属电池技术的重要进展。通过阐明和调控I-iLi的形成机制,该工作为研究锂损失现象提供了变革性的视角,为设计高度可逆的锂金属负极提供了关键见解。相关研究成果以“Revealing ionically isolated Li loss in practical rechargeable Li metal pouch cells”为题发表在Science Bulletin上。
三、研究亮点
1.概念上,揭示了离子孤立锂(I-iLi)的形成机制,拓宽了对实际贫电解液条件下锂损失形式和途径的理解,是对传统的电子孤立锂的重要补充。2.技术上,提出了电极润湿性的评估标准——电解液浸润率(EFR),该标准可推广应用于其他碱金属(如Na 和 K)电池或锂离子电池技术中。3.实践上,在原型1.4 Ah无负极NMC||Cu电池中同时实现了551 Wh kg-1的高电池级能量密度和100次循环后70%的容量保持率。
四、图文导读
1.离子孤立锂(I-iLi)的形成机制
概念上,揭示了离子孤立锂(I-iLi)的形成机制,拓宽了对实际贫电解液条件下锂损失形式和途径的理解,是对传统的电子孤立锂的重要补充。2.技术上,提出了电极润湿性的评估标准——电解液浸润率(EFR),该标准可推广应用于其他碱金属(如Na 和 K)电池或锂离子电池技术中。3.实践上,在原型1.4 Ah无负极NMC||Cu电池中同时实现了551 Wh kg-1的高电池级能量密度和100次循环后70%的容量保持率。
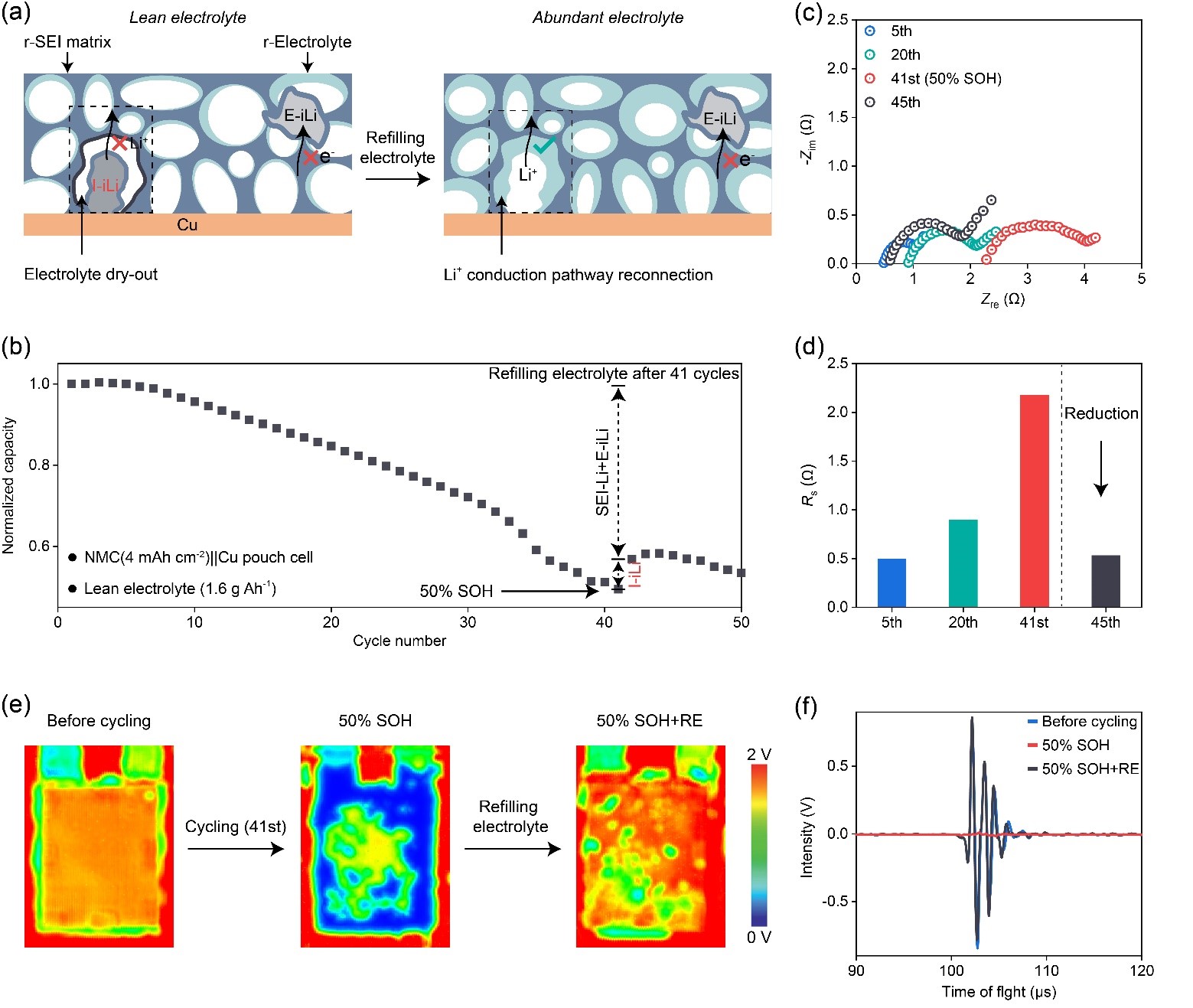
图1. 贫电解液条件下,锂金属软包电池负极中离子孤立锂(I-iLi)的形成。(a)I-iLi的产生和再激活示意图。(b)NMC||Cu叠片式软包电池在0.3 C倍率下循环时归一化电池容量与循环数的关系。循环到50%健康状态(SOH)时,再次注入足量电解液(6 g Ah-1)。(c)电池在第5、20、41(50% SOH)和45圈循环后的阻抗图,以及(d)相应的Rs(溶液电阻)拟合值。(e)电池在循环前以及50% SOH下重新注入电解液前后的超声波透射图,以及(f)相应的超声波曲线。
在重复的锂沉积/溶解过程中,锂金属负极会经历显著的周期性体积膨胀与收缩。这一现象在高比能锂金属电池中尤为突出,特别是对于面容量大于4 mAh cm-2的电极。整个过程中,不良的(电)化学反应不断消耗有限的活性锂和电解液,生成固体电解质界面相(SEI-Li)和电子孤立的死锂(E-iLi)。随着电解液的持续消耗和电极结构的逐渐松散,电极的润湿状态逐步恶化,导致负极侧在循环过程中不可避免地出现电解液退浸润现象。这破坏了锂离子传导通路,导致离子孤立锂(I-iLi)的形成。它是死锂的另一种形式,作为E-iLi的重要补充,进一步加剧了容量衰退(图1a)。补充电解液后,I-iLi能够通过恢复的锂离子传导通路而被激活,而E-iLi则依然被SEI包裹,无法与电子传输网络连接。因此,为了推动锂金属电池的实际应用,必须对I-iLi的含量以及SEI-Li和E-iLi的总含量进行定量分析。为确认I-iLi的存在并量化其含量,该研究采用了高比能无负极软包电池配置,进行电解质依赖性容量恢复实验。这种无负极架构使用4 mAh cm-2的NMC正极和铜集流体负极,电解液注入量为1.6 g Ah-1,电池级能量密度为506 Wh kg-1。实验中,电池在循环至50%健康状态(SOH)时,重新注入大量电解液(6 g Ah-1),观察容量恢复情况,以评估I-iLi的存在及含量。在此配置下,电池在循环过程中经历了快速的容量下降,仅41次循环后容量即下降至50% SOH,同时伴随电极/电解液界面快速恶化(图1b、c)。溶液电阻(Rs)在第5圈循环后为0.5 Ω,而在第41圈循环后增至2.2 Ω,表明电解液的严重分解和负极侧固液界面接触的减弱(图1d)。在50% SOH下重新注入电解液后,电池在第42圈循环中显示出明显的容量恢复(17.6 mAh),占总容量损失的15%。此外,溶液电阻在第45圈循环后降至接近初始值的0.5 Ω,表明电极润湿状态恢复。这些现象有力地证实了I-iLi的存在,并表明其可以通过电解液介导的离子通路修复重新激活。作为对比,当将初始电解液剂量增加至6 g Ah-1并进行相同处理时,重新填充电解液后的电池容量仅恢复2.1 mAh(占总容量损失的3%),且Rs值几乎没有变化。这些差异表明,I-iLi的形成源于固液界面接触的恶化,并且其对实际贫电解液条件下电池性能的影响显著。为进一步验证电解液退浸润诱导的I-iLi形成过程,该研究在图1b所示的电池循环过程中同步应用无损超声成像技术,以直观反映电池运行过程中电极润湿状态的演化。经过真空处理以消除气体影响后,超声波透射率从高到低被转换为红到蓝的热图,其中蓝色代表界面接触较差。原始状态下的软包电池超声图像呈均匀的浅红色,表明电池内部润湿状态良好(图1e)。然而,循环至50% SOH后,超声图像中出现了大面积的蓝色区域,表明电池内部界面接触的明显退化(图1f)。值得注意的是,重新填充电解液后,蓝色区域几乎消失,表明固液界面接触恢复。这一现象与电池容量和溶液电阻恢复的结果一致,进一步验证了电解液降解驱动的I-iLi形成机制。
2.不同压力下I-iLi含量的变化
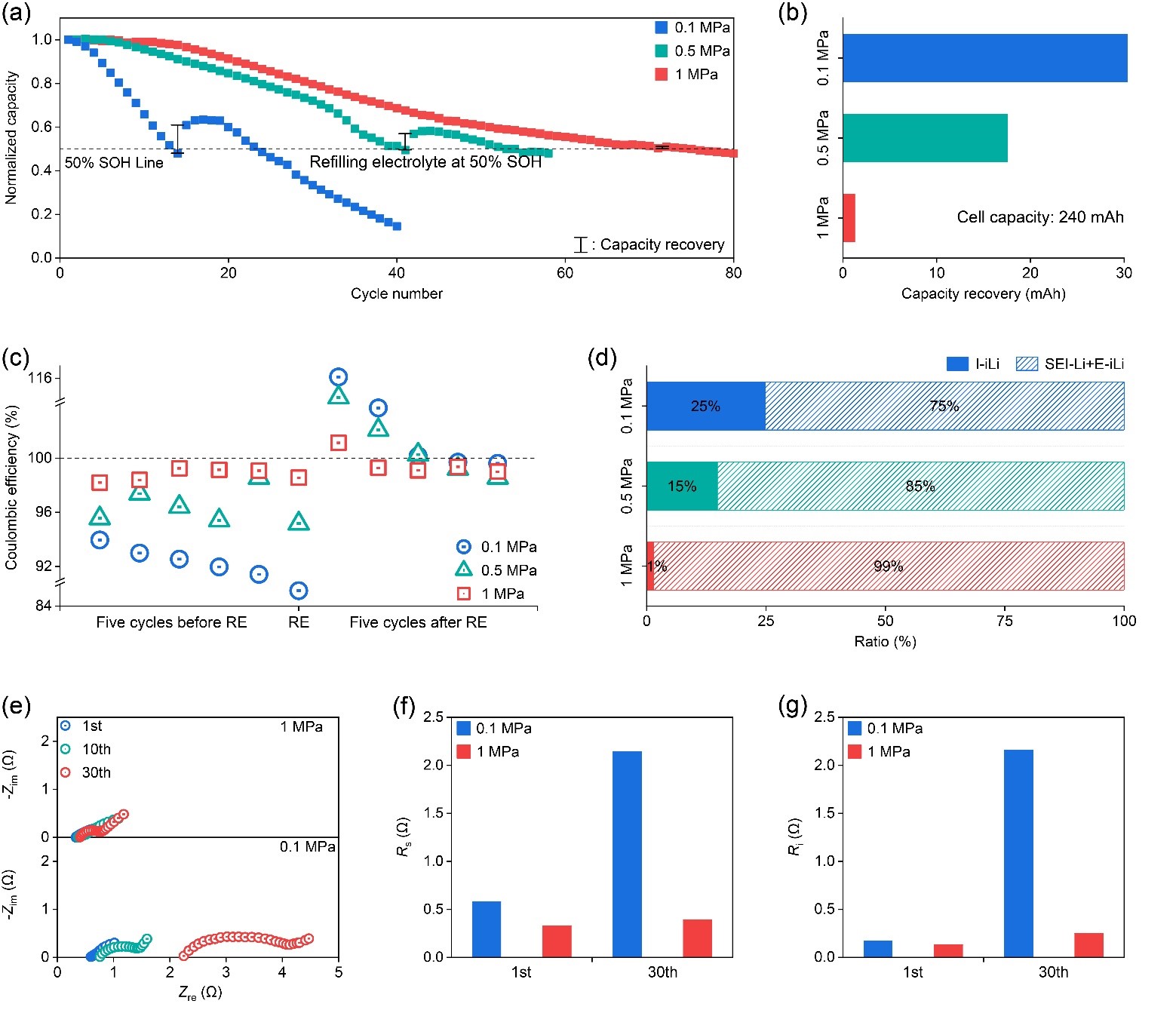
图2. NMC||Cu软包电池在不同压力下循环过程中I-iLi的含量变化。(a)NMC||Cu叠片式软包电池在0.1、0.5和1 MPa下以0.3 C倍率循环时归一化电池容量与循环数的关系,以及相应的(b)在50% SOH下重新填充电解液(6 g Ah-1)后的容量恢复。(c)电池在不同压力下循环过程中的库仑效率(CE)。(d)电池在不同压力下循环至50% SOH时内部I-iLi占总锂损失的比例。(e)电池在0.1和1 MPa压力下循环过程中的阻抗图,以及第1次和第30次循环后的相应的(f)Rs值(表示溶液电阻)和(g)Ri值(表示界面电阻)。
受到外部压力在抑制E-iLi形成方面的显著作用启发,该研究探讨了外部压力(0.1至1 MPa)对I-iLi含量及电化学性能的影响。在0.1、0.5和1 MPa外压下,240 mAh级NMC||Cu软包电池展现出不同的循环稳定性,其容量分别在14、41和71次循环后衰减至初始值的50%(图2a)。随着外部压力的增加,电池的循环寿命和库仑效率(CE)逐步提高,表明有效的压力调节能够显著减缓锂损失及电池退化。同时,在50% SOH下重新注入电解液(6 g Ah-1)后,这些软包电池的容量恢复情况从30.4 mAh降至1.2 mAh(图2b)。其中,在0.1 MPa下循环的电池在电解液重新填充后的第一个循环中表现出最高的CE,达到116%,比填充前高出30.1%。在0.5 MPa下循环的电池,再次注入电解液后CE增加了17.7%,达到112%以上(图2c)。这些现象证明了I-iLi的形成是电池容量衰减的一个重要原因,并且该部分容量损失可以通过重新连接离子通路来进行修复。相比之下,1 MPa下运行的电池,其CE在电解液补充前后的变化仅为2.5%,这一变化与最低的容量恢复一致,表明电池内部电解液的衰退得到了显著缓解。因此,I-iLi占总锂损失的比例从0.1 MPa下的25%降低至1 MPa下的1%(图2d),同时电池寿命得以延长。以上结果表明,在锂金属电池重复的电镀/剥离过程中,压力调节有助于维持离子/电子渗透网络的完整性。
3.电解液浸润率(EFR)标准评估电极润湿性
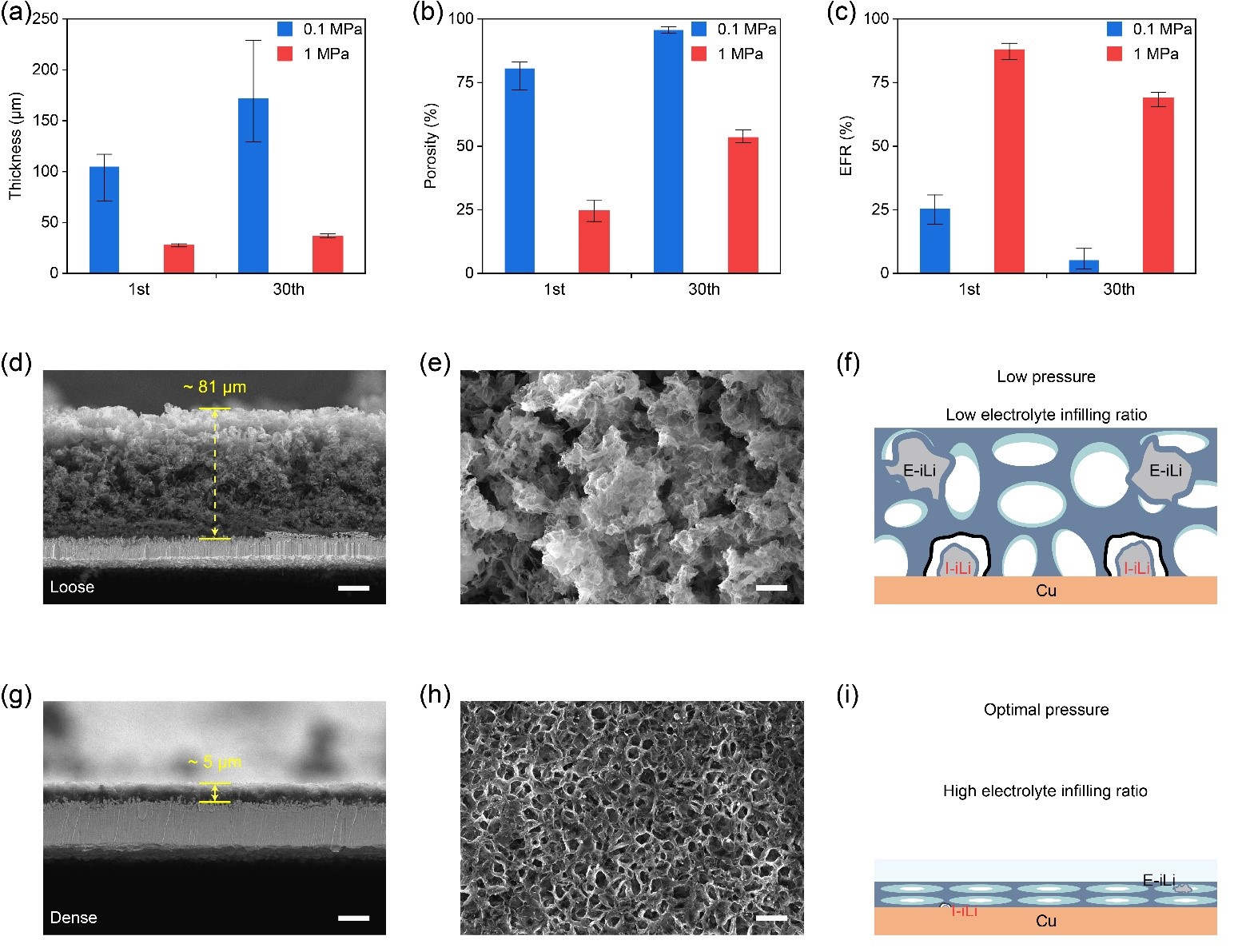
图3. 电解质浸润率(EFR)作为评估电极/电解液界面润湿状态的指标。(a-c)在0.1和1 MPa外压下NMC||Cu软包电池循环过程中锂沉积物的(a)厚度,(b)孔隙率,和(c)EFR值。(d-e)0.1 MPa下首次放电后电池中负极的(d)表面SEM图像和(e)截面SEM图像。(f)低外压下循环的电池内部低EFR环境示意图。(g-h)1 MPa下首次放电后电池中负极的(g)表面SEM图像和(h)截面SEM图像。(i)优化外压下循环的电池内部高EFR环境示意图。
为探索压力调控背后的影响机制,该研究首次引入电解质浸润率(EFR)作为评估电极/电解液界面健康状况的直接指标。锂金属负极的EFR值取决于锂沉积物的孔隙率和电解液残余量,可通过负极内已浸润孔体积与总孔体积的比率来定量表示,其中孔隙率的提高和电解液的衰退会导致EFR值降低。在0.3 C下首次充电后,0.1 MPa下的NMC||Cu软包电池中的锂沉积物厚度达到104.8 μm(根据六个不同位置的统计学结果),是具有相同锂容量的致密金属锂(20 μm,4 mAh cm-2)厚度的五倍(图3a)。这种巨大的差异源于低压下无序的锂沉积行为,导致电池负极侧的高孔隙率(81.1%)和低EFR值(25.4%)(图3b、c)。劣质的锂沉积行为和较差的界面浸润状态会进一步恶化电池的循环性能,经过30次循环后,锂沉积层显著增厚(172 μm),孔隙率增加(95.6%),EFR值下降至5.2%。这种高度多孔的电极结构和不良的电极/电解液界面接触共同破坏了电池内部离子/电子传导网络,导致电池快速失效。相比之下,在1 MPa下首次充电后形成的锂沉积物的厚度为27.5 μm,接近具有相同锂容量的完全致密金属锂箔的厚度(21 μm,4.2 mAh cm-2),表明电池内发生了高度致密的锂沉积行为,负极孔隙率降低至24.7%,EFR值升至87.8%。致密的电极结构有效抑制了活性锂与电解液之间的不良反应,保持了离子和电子的有效传导,从而提高了电化学循环稳定性。经过30次循环后,与0.1 MPa下情况相比,1 MPa下的锂沉积物的厚度(36.5 μm)显著减薄,孔隙率显著下降(53.3%),EFR值大幅升高(68.9%)。
通过对放电状态下软包电池内锂金属负极的结构和形貌进行表征,该研究进一步揭示了压力调控与EFR增加之间的关系。0.1 MPa下,NMC||Cu软包电池首次锂溶解后,Cu集流体上留下了一层81 μm厚的疏松副产物层,该层由絮状SEI膜和死锂组成(图3d、e)。这一现象表明,放电过程中电池内部发生了严重的寄生反应,导致大量活性锂和电解液的消耗。在循环过程中,这一厚而多孔的副产物层显著阻碍了离子/电子传输通路,致使电极的润湿状态迅速恶化。由此产生的低EFR电化学环境进一步引发了SEI和死锂(包含E-iLi和I-iLi)的快速生成,进而加剧了锂的消耗和电池容量的退化(图3f)。在1 MPa的优化压力下,首次循环后形成的副产物层显示出均匀致密的结构,厚度为5 μm(图3g、h)。这种优良结构源于高度可逆的锂沉积/剥离行为,能够有效抑制副反应并确保电极界面的良好润湿。这使得电池在恶劣条件下运行期间,锂和电解液的衰减得到了明显改善,维持了电池内部高EFR环境,有效地保护了离子/电子的传导网络,避免了电化学反应通路的切断(图3i)。
4.不同压力下电解液的演化
利用19F NMR光谱分析,该研究量化了在不同压力下循环的NMC||Cu软包电池内电解液的衰退情况。由于FEMC(~ -79 ppm)和HFE(~ -76、-93和-137 ppm)溶剂在19F NMR光谱中的峰位存在重叠(均含有CF3CH2O-基团),因此在后续分析过程中将二者合并,统称为FEMC+HFE。为了进行定量分析,研究中使用六氟苯(C6F6)试剂作为内部参照物。在0.1 MPa下以0.3 C循环30圈后,软包电池内电解液出现了明显的降解,19F NMR光谱中LiPF6(~ -70 ppm)和LiDFOB(~ -150 ppm)的信号完全消失,FEC(~ -122 ppm)和FEMC+HFE的强度也显著减弱(图4a)。与原始电解液的19F NMR光谱相比,循环后电解液中的LiPF6和LiDFOB几乎完全消耗,FEC(保留率为47%)和FEMC+HFE(保留率为60%)也被严重消耗。这一现象源于0.1 MPa下恶化的锂电镀/剥离行为,导致有限的电解液被迅速消耗(图4b)。相较之下,在1 MPa下循环30圈后,电解液中的各含F组分保留率较高:LiPF6(72%)、LiDFOB(70%)、FEC(82%)、FEMC+HFE(93%)。以上结果表明,通过优化压力,循环过程中电池电解液的降解得到了有效抑制,从而保持了高EFR环境,并减少了高比能电池中I-iLi和E-iLi的生成。为了进一步证实压力优化抑制了副反应,该工作对第30次放电后负极侧的残留物进行了电子探针(EPMA)微分析。在0.1 MPa下,残留副产物层的厚度高达122 µm,结构上充满裂纹,F元素的分布不均,表明循环过程中发生了严重的寄生反应(图4c)。这一厚且不均匀的副产物层由SEI和死锂组成,严重阻碍了电池内部电化学电路的畅通,导致电池阻抗增加和EFR值降低。值得注意的是,在1 MPa下经过30次循环后,Cu集流体上观察到了一层厚度为16 µm的均匀完整的反应层,F元素分布均匀(图4d),表明电解液分解得到了有效抑制,电极-电解液界面保持了良好接触。这确保了循环过程中电池内部的高EFR环境的维持,保护了离子/电子渗透网络,从而减少了因电子/离子隔离导致的死锂的形成。
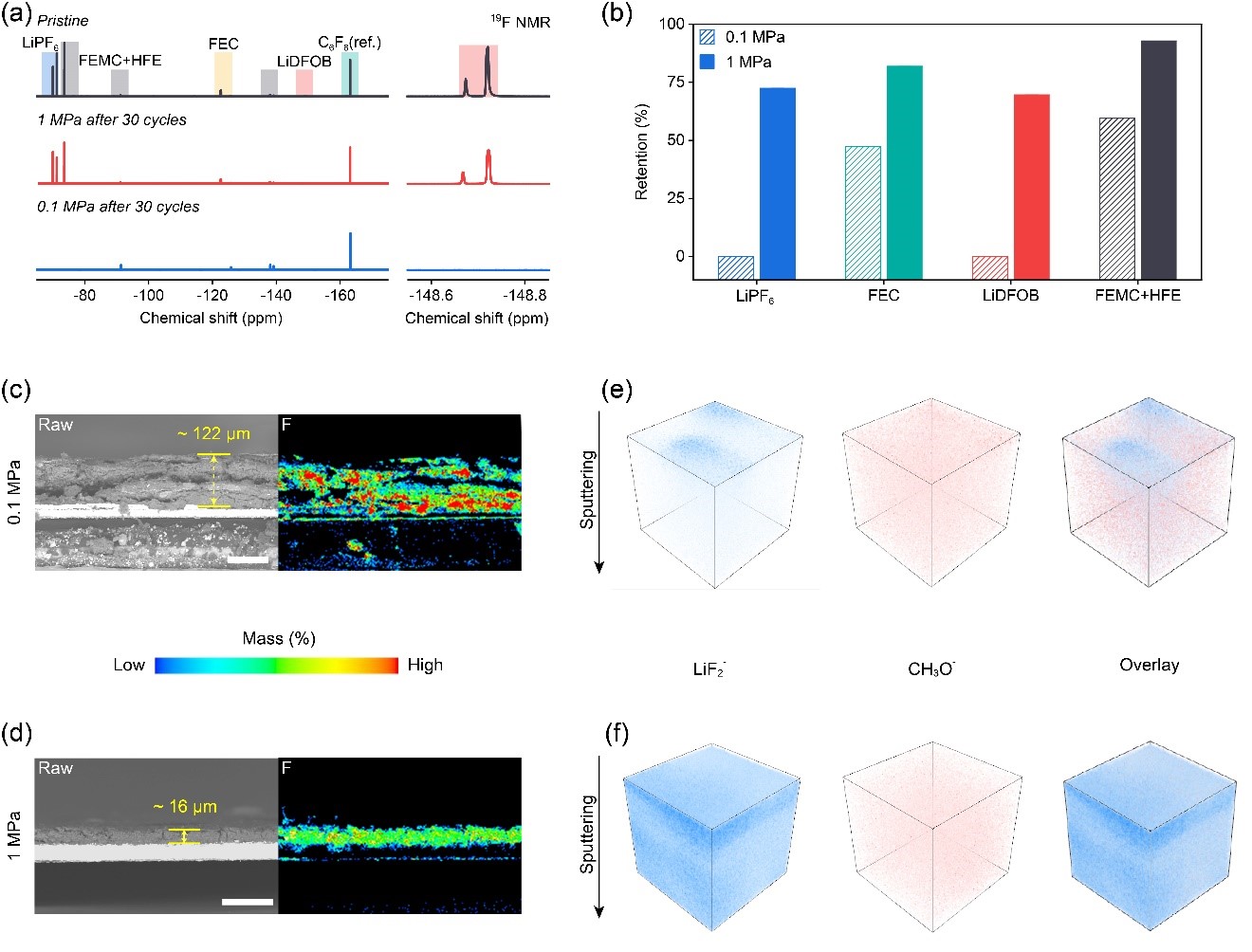
图4. 不同压力下循环过程中NMC||Cu软包电池内的电解液演化。(a)原始电解液和分别在0.1和1 MPa下经过30次循环后的NMC||Cu软包电池电解液的19F NMR谱图。(b)在0.1和1 MPa下经过30次循环后的电池电解液中含F成分的保留情况汇总。以六氟苯为内参进行定量分析。(c,d)在(c)0.1和(d)1 MPa下经过30次循环后的电池负极的截面BSE图像和对应的F元素映射图像。(e,f)在(e)0.1和(f)1 MPa下经过30次循环后的电池负极上SEI成分的三维分布图像。
利用飞行时间二次离子质谱(ToF-SIMS)深度蚀刻技术,进一步解析了SEI膜的三维纳米结构。LiF2-和C3HO-分别是来源于LiF和有机成分的特征离子碎片,其中LiF被确定是SEI中优选且不可或缺的组成成分。在0.1 MPa下循环30圈后,电池负极表面形成了一层不规则的SEI层,其特征为LiF含量低且分布无序,主要成分为有机化合物(图4e)。这种富含有机物且不均匀的SEI层难以在电池运行期间稳定电极/电解液界面,也不能有效抑制电解液渗透到电极内部。相比之下,在1 MPa外压下形成的SEI层呈现出均匀的LiF分布,其强度明显高于0.1 MPa压力下形成的SEI层(图4f)。这种有利的SEI结构有助于均匀化电化学反应,并钝化电极/电解液界面,从而提升电池的稳定性。
5.Ah级软包电池应用实例
为强调EFR标准在实际电池系统中的重要性,该研究采用了4 mAh cm-2的高正极负载、零过量锂和1.4 g Ah-1的贫电解液剂量等关键参数,成功制造了具有极高能量密度的原型1.4 Ah NMC||Cu软包电池(图5a)。0.1 MPa下,电池在0.2 C下仅循环40圈后,容量保持率便下降到67%,同时伴随显著的电压滞后和内阻增加(图5b、d)。相比之下,在1 MPa下循环的电池分别在0.1和0.2 C下提供了1.49和1.45 Ah的容量,分别对应于551和530 Wh kg-1的超高电池级能量密度。此外,Ah级NMC||Cu软包电池在1 MPa下展现出稳定的循环性能,0.2 C下经过100次循环后仍保持70%的容量。同时,溶液和界面的阻抗,以及固液界面接触状态在整个循环过程中均未出现明显退化。上述结果强调了维持高EFR环境和最小化I-iLi生成对于提升高比能可充电电池系统稳定性的重要性。
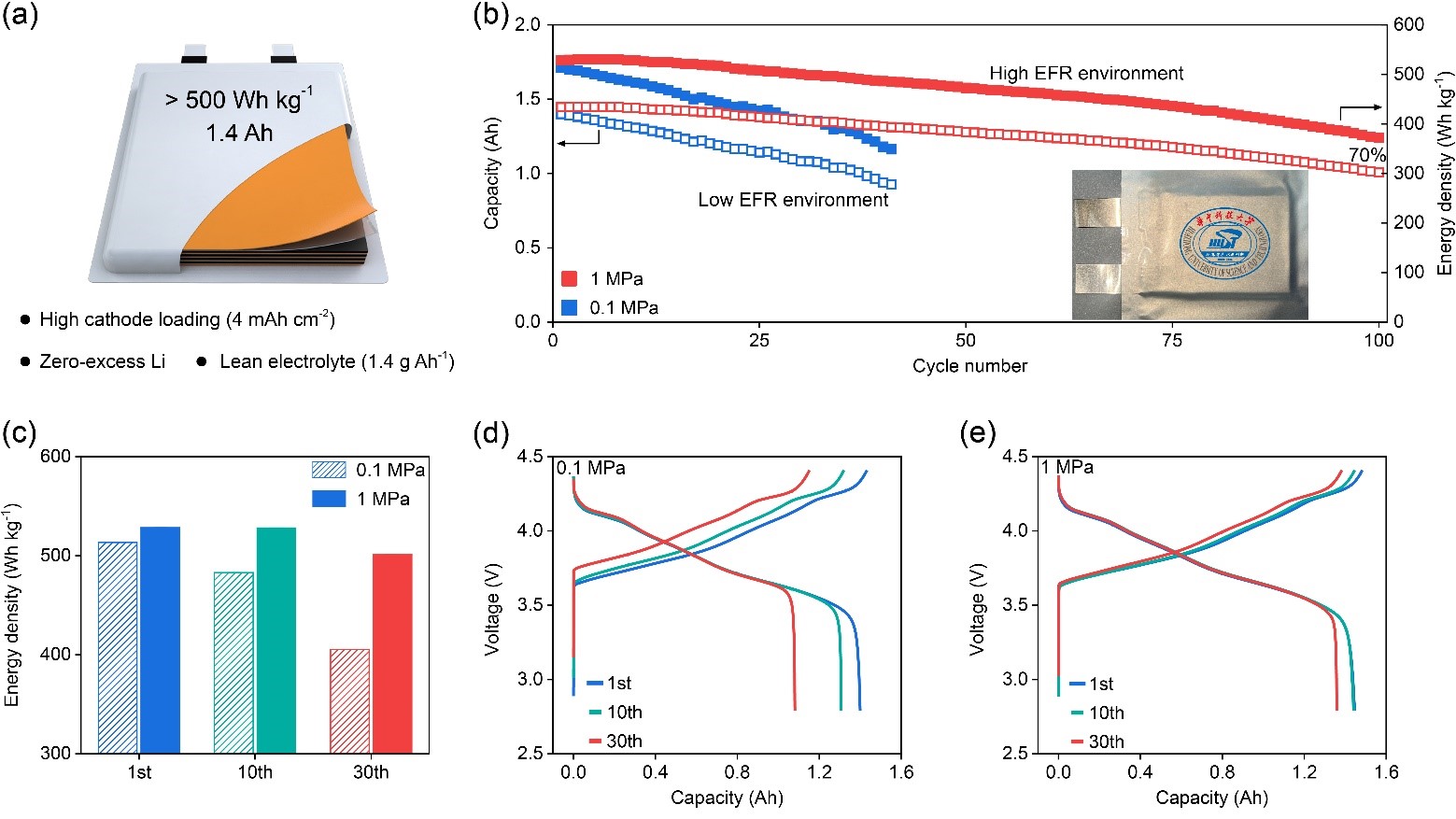
图5. 不同压力下原型1.4 Ah NMC||Cu软包电池的电化学性能。(a)Ah级无负极电池配置的关键参数。(b)0.1和1 MPa下1.4 Ah NMC||Cu软包电池的容量和能量密度与循环数的关系。(c)0.1和1 MPa下的电池在不同循环圈数后能量密度比较。(d,e)分别在(d)0.1 MPa和(e)1 MPa压力下循环的电池在不同循环圈数时的电压曲线。
五、结论展望
综上所述,本文定量分析了高比能锂金属软包电池在特定健康状态下电解液依赖的容量恢复特性,揭示了锂金属负极中一种与传统的电子孤立锂(E-iLi)不同的新形式“死锂”——离子孤立锂(I-iLi),提出了电极润湿性的评估标准——电解液浸润率(EFR)。进一步引入应力调节来致密化负极结构、减缓电解液消耗,从而维持高EFR环境并抑制I-iLi的形成,最终在安时级无负极NMC||Cu软包电池中同时实现了551 Wh kg-1的高能量密度和稳定的循环性能。这项工作深入阐明了贫电解液下“死锂”的形成机制,揭示了其新的存在形式,为锂损失机制的调控提供了变革性的视角,为设计高度可逆的锂金属负极提供了重要的理论指导。