近日华中科技大学孙永明教授和杨辉教授课题组合作在Energy & Environmental Materials上发表了题为“Stress-Regulation Design of Lithium Alloy Electrode towards Stable Battery Cycling”的研究论文。作者通过机械压印和化学预锂化方法,在引入活性锂的同时在箔材合金负极表面构筑了用于应力调控的微区波状结构,制备出微区波状锂锡合金/锡(LiSn/Sn)电极。波状结构可以快速弛豫因电极体积膨胀产生的应力,有效地延缓了合金电极的电化学-力学失效。化学预锂化提供额外的锂源用于弥补循环过程中的锂损失,极大地提高了锡箔在全电池使用中的能量密度和循环寿命。所制备的微区波状LiSn/Sn电极的首圈库仑效率高达95%,对称电池在循环1000小时后依然稳定运行,LiNi0.6Co0.2Mn0.2O2||LiSn/Sn电池在0.5 C的电流密度下展示出2.4 mAh cm-2的可逆面容量,并且在100次循环后保持85%的容量。这项工作提出了一种解决合金负极中机械应力引起的电极失效和同步实现锂补偿的策略,为实现合金箔材负极在锂离子电池中的实际应用提供了一种新的思路。
近年来,人们对锂离子电池等能源存储器件的能量密度及功率密度不断提出更高的需求。商用锂离子电池中的石墨负极的理论比容量仅为372 mAh g-1,极大限制了锂离子电池的能量密度。合金锡负极通过与金属锂形成锂锡合金具有较高的理论比容量(994 mAh g-1)。然而锡负极在充放电过程中会发生较大的体积变化,引起电极的破裂和活性材料的剥落,导致电池循环稳定性劣变。过往的研究通过设计纳米结构或者引入非活性组分构筑复合结构来缓解合金锡负极的体积膨胀问题,然而目前纳米材料本征的特点(比表面积高、压实密度低、制备方法复杂等)带来了电极副反应加重、制备成本高等问题。纳米结构和非活性材料的引入均会降低电池的能量密度。与传统的颗粒电极不同,金属锡箔具有很好的机械加工性、高体积能量密度等优势,然而金属锡箔在循环过程中也会因电极体积膨胀/收缩变化会发生应力分布不均匀的问题,导致电池循环初期活性锂损失严重,库伦效率极低;以及后续循环中电极容易发生电化学-力学失效,电池循环稳定性变差。
本工作中,作者通过简单的机械压印方法在金属锡箔表面设计了一种微区波状结构,并对电极进行同步化学预锂化。微区波状结构有助于在电极合金化和去合金化过程中产生的应力的快速弛豫,有效缓解了电极的电化学-力学失效;预先合金化形成的含锂合金层不仅能有效补偿锂离子电池在首次和循环过程中的锂损失,同时其预膨胀的结构也有助于改善电极内的应力集中。此外,活化的锂合金层结构有利于电极循环过程中的均匀化电化学反应。通过控制预锂化剂与金属锡箔的反应时间,可以实现预嵌锂量的准确控制。电极形貌及成分分析表明,微区波状LiSn/Sn的结构尺寸及其表面形成的LiSn合金层厚度均匀可控。由于活性锂的额外引入,微区波状LiSn/Sn电极具有极高的首圈库伦效率(95%),所组装的对称电池在1 mA cm-2、1 mAh cm-2的条件下循环1000小时以后依然保持着极低的过电位。进一步通过电化学-力学模拟发现,微区波状能够有效地调控LiSn/Sn电极在嵌锂/脱锂过程中所产生的应力,而未经处理的锡箔则由于应力无法得到有效的缓解而产生开裂甚至破碎。在微区波状应力调控结构和LiSn合金额外补锂的协同效应下, 由三元高镍正极和该负极组成的电池(LiNi0.6Co0.2Mn0.2O2||LiSn/Sn)下展示出高的(2.4 mAh cm-2)可逆面容量,并且在100次循环后容量保持率高达85%。而使用纯锡箔的对比电池在同等测试条件下可逆容量仅为0.3 mAh cm-2。这项工作提供了一种同步解决合金箔材电极电化学-力学失效和库伦效率低的方法,展示了合金箔材电极在高比能锂离子电池中的应用潜力。
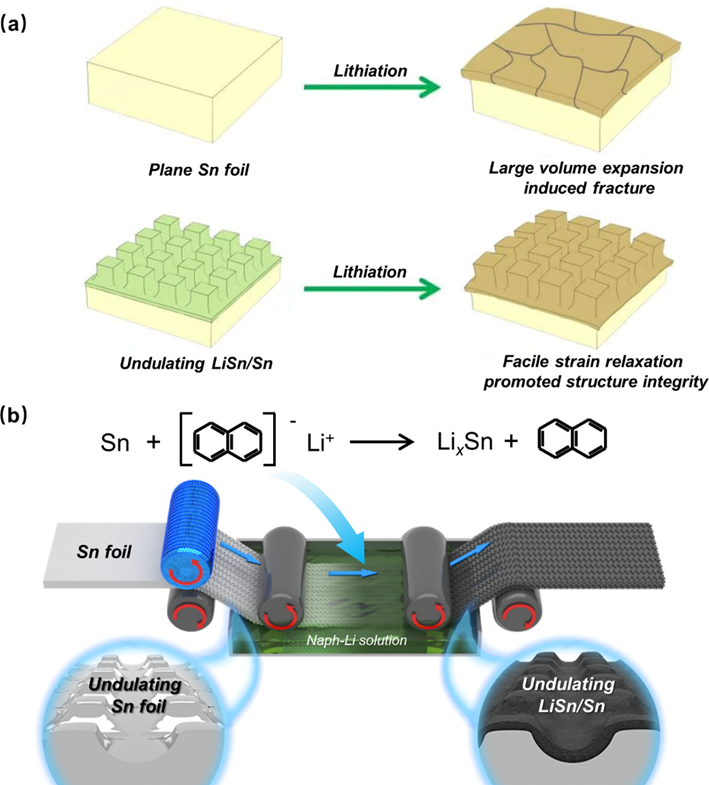
图2-1微区波状LiSn/Sn电极的示意图:(a)Sn平面电极和微区波状LiSn/Sn电极的结构示意图,(b)微区波状LiSn/Sn电极的制备过程示意图。
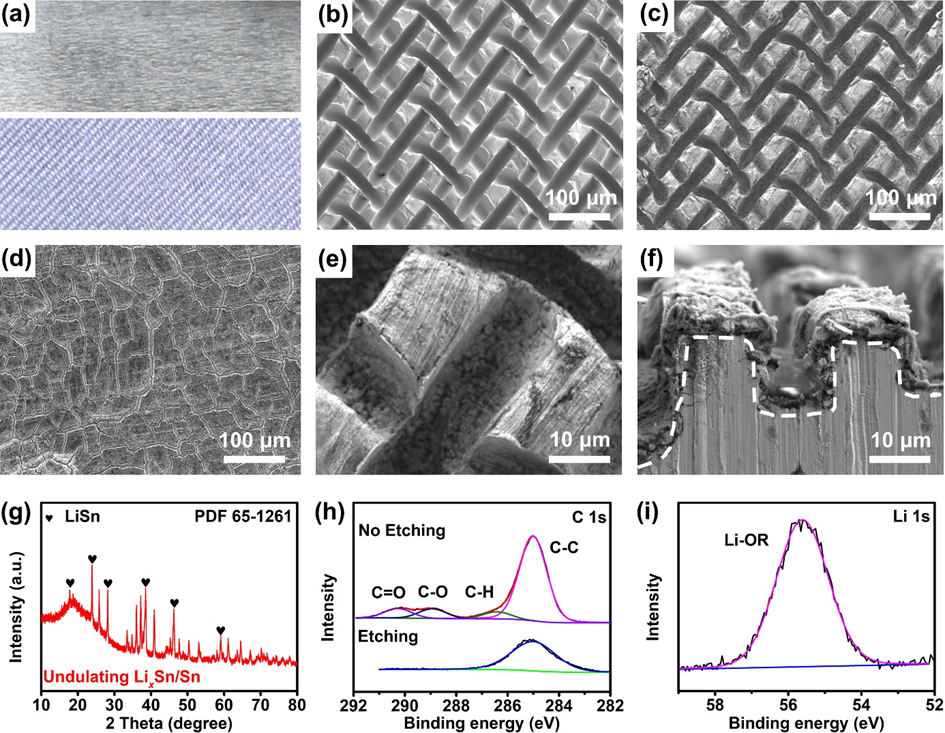
图2-2微区波状LiSn/Sn电极的表征:(a)Sn平面电极和微区波状Sn电极的光学照片;(b、c、d)微区波状Sn电极、微区波状LiSn/Sn电极和LiSn/Sn平面电极的低倍扫描电镜图;(e、f)微区波状LiSn/Sn电极表面和截面图高倍扫描电镜图;(g)微区波状LiSn/Sn电极的XRD图谱;(h)微区波状LiSn/Sn电极在Ar+离子刻蚀前后的XPS高分辨C1s谱;(i)微区波状LiSn/Sn电极的XPS高分辨Li 1s谱。
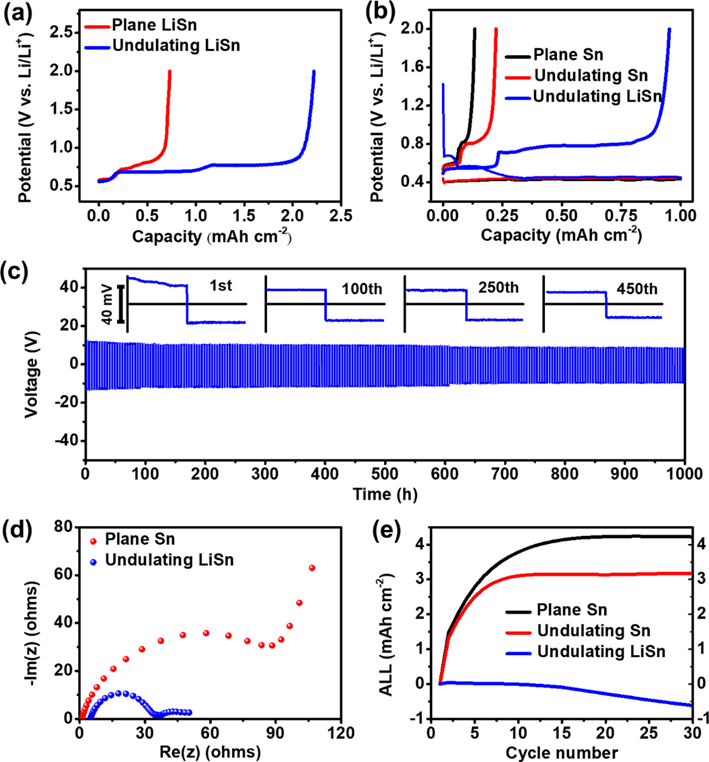
图2-3微区波状LiSn/Sn电极的电化学性能:(a)微区波状LiSn/Sn电极和平面LiSn/Sn电极的电化学脱锂曲线;(b)平面Sn电极、微区波状Sn电极和微区波状LiSn/Sn电极的首次循环电压-容量曲线;(c)由微区波状LiSn/Sn电极组成的对称电池在1mA cm-2、1mAh cm-2的条件下的电压-时间图;(d)平面Sn电极和微区波状LiSn/Sn电极循环前的EIS阻抗图;(e)平面Sn电极、微区波状Sn电极和微区波状LiSn/Sn电极在0.25mA cm-2、1 mAh cm-2的条件下前三十次循环的累积锂损失量。
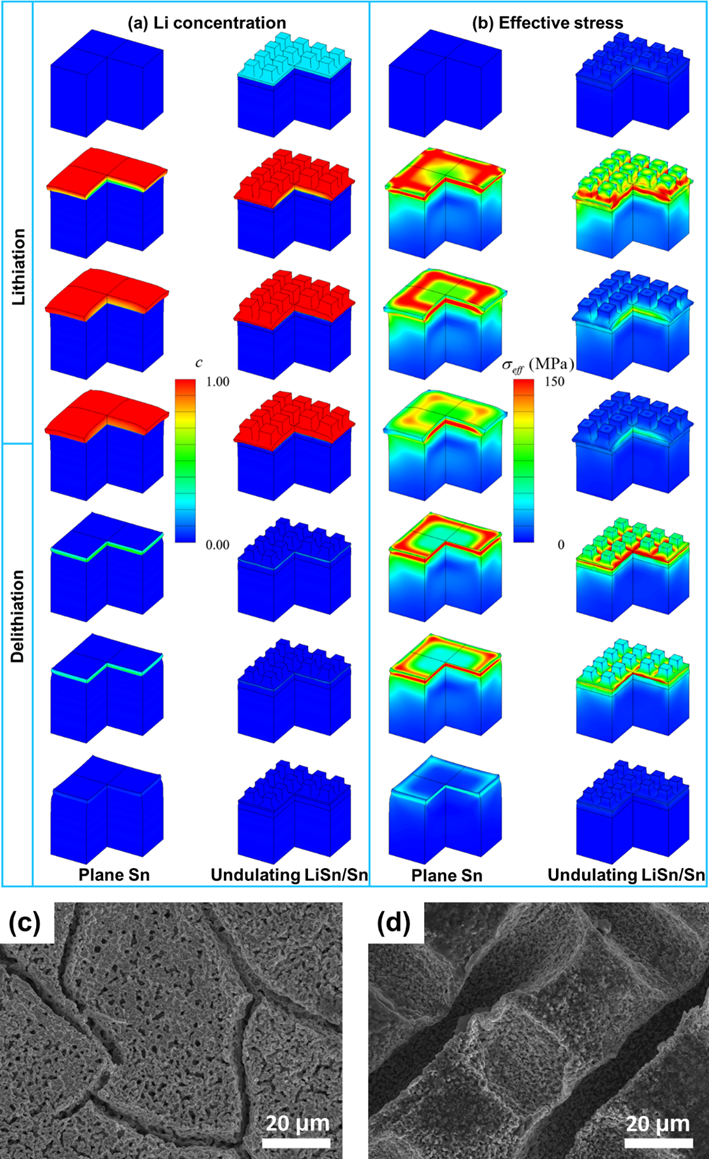
图2-4微区波状LiSn/Sn电极电化学-力学耦合模拟:(a、b)平面Sn电极和微区波状LiSn/Sn电极在不同锂化阶段的电化学-力学耦合模拟图:(a)Li浓度分布和(b)应力分布;(c、d)平面Sn电极和微区波状LiSn/Sn电极在30次电化学循环后的扫描电镜图。
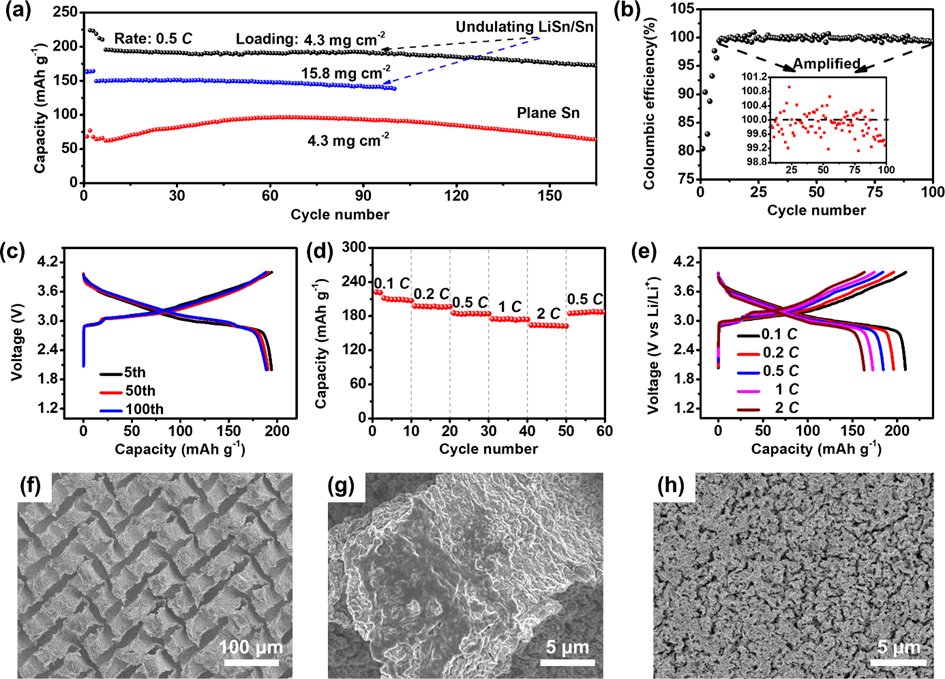
图2-5 NCM622||微区波状LiSn/Sn电池和NCM622||平面Sn电池的电化学性能测试:(a、b、c)使用不同载量NCM622正极的全电池的循环性能和库伦效率;(d、e)不同倍率下的容量-循环曲线及对应的电压-容量曲线;(f、g、h)100次循环后微区波状LiSn/Sn电极和平面Sn电极的扫描电镜图。